Технологическая сигнализация
Сердцем технологической сигнализации являются RSтриггер и не важно, на какой базе это реализовано. Триггеры фиксируют все приходящие аварийные сигналы, которые в дальнейшем надо просто логически сгруппировать: на сигналы экстренной остановки работы котельной и на сигналы предупреждающие. К сигналам экстренной остановки работы котельной относятся:
— авария по CH4 (Метану);
— авария по СО, второй порог (Двуокись углерода);
— авария по пожару;
— авария по давлению в системе;
— авария по min/max давлению газа;
— авария по повышению/понижению, пропаданию фазы, питающей сети.
При появлении сигналов экстренной остановки следует в первую очередь отключить работающие горелки котлов и через 2-3 сек. произвести отключение главного газового электромагнитного клапана. К предупреждающим
сигналам относятся:
— авария по СО, первый порог;
— авария котла;
— охранная сигнализация.
При появлении предупреждающих сигналов следует предпринять соответствующие меры.
Все это удобно реализовать на простом свободно Программируемом Логическом Контроллере (ПЛК) Mitsubishi серии Alpha с питанием от Резервированного Источника Питания 24В (РИП 24). Такой подход позволяет всегда легко изменить алгоритм работы технологической сигнализации программным способом.
Сигналы на входы ПЛК надо подавать сформированными, т.е. логическая «1» равна +24В, а логический «0» — это либо минусовой провод, питающий контроллер, либо полное отсутствие сигнала (вход контроллера «висит» в воздухе). Это легко реализовать используя «сухие» контакты с датчиков (приборов) аварийной сигнализации. Все логические элементы контроллера называются Функциональные Блоки (ФБ). Так же можно создать Пользовательский Функциональный Блок (ПФБ) из нескольких ФБ. Как было описано выше (в данном случае) мы имеем 9 аварийных сигналов. Для их обработки используем девять RS триггеров.
Входы SET триггеров соединяем с входными клеммами ПЛК. Это могут быть входы I1-I9. Входы сброса (RESET) всех 9-ти триггеров объединяем вместе и соединяем их с входом ПЛК I10. Этот вход контроллера будет использоваться для ручного сброса аварийных сигналов. Для простоты схемы всю эту «матню» из 9-ти триггеров лучше собрать в ПФБ. На рис.1 видно 9-ть RS триггеров, а на рис.2 эти триггеры объединены в ПФБ, он меньше занимает места на экране и проще в программировании.

Далее сформируем из этих 9-ти сигналов сигнал для экстренной остановки работы котельной. Тут нам понадобится элемент OR (логическое сложение) с 6-ю входами, а в контроллере элементы OR имеют только 4 входа. Но это легко сделать объединив два элемента OR, как показано на рис.3. А еще лучше, если эти два элемента OR поместить в ПФБ (см. рис. 4).

На рисунке 5 можно видеть простую схему из 9-ти RS триггеров (объединенных в ПФБ1) и двух элементов OR (объединенных в ПФБ2). Выход ПФБ2 на двух элементах OR следует соединить с выходом ПЛК Q1 и использовать как аварийный сигнал для экстренной остановки работы котельной.
Для формирования сигнала предупреждение нам опять понадобится элемент OR (ФБ1). Входы ФБ1 следует соединить с выходами соответствующих RS триггеров сигнала предупреждение, а ФБ1 объединить с выходом ПФБ2 при помощи ФБ2 и его выход соединить с выходом ПЛК Q2. При данной схеме мы имеем на выходе контроллера два сигнала:
Q1 — сигнал экстренной остановки котельной;
Q2 — сигнал для включения общей световой и звуковой сигнализации аварии.

Но поскольку количество выходов ПЛК ограничено, то нам следует зашифровать аварийные сигналы. Что бы зашифрованные сигналы были легко читаемы и понятны, надо поступить следующим образом:
Выходной сигнал авария «Метан» с выхода ПФБ1 подать на вход ФБ3 (OR), выход ФБ3 соединить с выходом ПЛК3 Q3. На второй вход ФБ3 подать сигнал авария «Сеть». Этот сигнал надо взять с соответствующего выхода ПФБ1 и соединить его с входом нового ФБ8 Flicker, выход сигнала ФБ8 надо подать на второй вход ФБ3. ФБ Flicker работает следующим образом:
При появлении на входе сигнала (логич. «1») он начинает генерировать импульсы. Частоту и длительность импульсов можно задать в setup-е ФБ. Для нашего случая частоту следования импульсов следует задать где то 2 Гц со скважностью 2 (меандр). При данном схемном решении у нас получится:
При появлении сигнала авария «Метан», н.р. контакты ПЛК (Q3) переключатся в н.з. и будут в этом состоянии до тех пор, пока не будет нажата кнопка «Сброс» (вх. ПЛК I10);
При появлении сигнала авария «Сеть» н.р. контакты ПЛК (Q3) будут с частотой в 2 Гц замыкаться и размыкаться.
При такой организации шифрования сигнала на выходе ПЛК Q3 ясно и наглядно видно, что если световой индикатор горит постоянно, то произошла авария «Метан»; если световая индикация мигает (2 Гц), то произошла авария «Сеть». Этим мы сэкономим в 2 раза «драгоценные» выходы ПЛК.
Другие аварийные сигналы надо выполнить соответствующим образом.
Оставшиеся входы и выходы ПЛК можно использовать для автоматической подпитки системы, как было описано выше, в статье «Автоматическая система подпитки на базе контроллера Mitsubishi серии Alpha».
Для создания простейшей удаленной диспетчеризации достаточно параллельно световой индикации аварий, подключить через телефонный кабель дополнительную панель аварийных сигналов.
Куликов В.Н.
E-mail: atm@sura.ru.

В данной публикации описываются широко используемые гидравлические схемы водогрейных котельных, их достоинства и недостатки, а так же возможности автоматизации этих схем. Совершенствование гидравлических схем, точнее, преобразование одной схемы в другую более качественную, надежную и легко управляемую.
Всем известна традиционная классическая гидравлическая схема водогрейной котельной (далее классическая схема), показанная на рисунке 1, - "рождение" ее было связано с появлением первых котлов, и на протяжении долгого времени была неизменной. Естественно, эта гидравлическая схема не отвечает современным требованиям, предъявляемым заводами изготовителями котлов и техническим возможностям настоящего времени. Одни из существенных недостатков классической схемы это:
1. отсутствие возможности поддержания определенной минимальной температуры теплоносителя на входе котла. Это одно из требований заводов изготовителей котлов;
2. схема имеет переменный проток воды через котлы, т.е. во время ремонтных либо профилактических работ котел отсекается от системы своей запорной арматурой, объем воды нагнетаемый насосом распределяется через оставшиеся котлы, при этом меняется гидравлическое сопротивление котельной и соответственно температурный график, а это уже явное отклонение от проектных расчетов, что существенно сказывается на общем КПД котельной;
3. не качественное регулирование теплоносителя в нагрузках. В настоящее время управление нагрузками осуществляется 3-х (4-х) ходовыми смесителями совместно с погодозависимыми регуляторами температуры.
Не зря же все стремятся заставить работать двигатель внутреннего сгорания на одних постоянных оборотах, при постоянной рабочей температуре и при этом иметь переменную нагрузку, при такой работе двигателя можно получить максимальный КПД работы, но об этом после.
В теплотехнике нагрузки практически всегда имеют переменный характер работы, как по температуре теплоносителя, так и по протоку теплоносителя, но нам надо, что бы это никак не влияло на температуру теплоносителя в котле и на проток теплоносителя через котел.
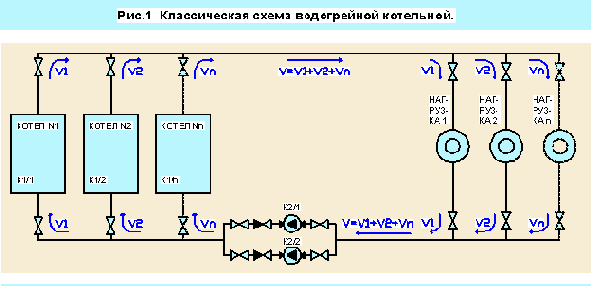
То что насосы стоят в обратной линии (см. рис. 1) связано только с тем, что отечественные насосы серии К (раньше широко применялись) по паспорту могут перекачивать теплоноситель с температурой до 70оС. Где стоят насосы, в обратной или подающей линии зависит от проектных решений и удобства монтажа, главное что бы насосы по паспорту выдерживали температуру теплоносителя, было обеспечено подпорное давление и производительность насосов должна соответствовать паспортным данным.
Согласно СНиП II-35-76 "Котельные установки" и СП 41-104-2000 "Проектирование автономных источников теплоснабжения", котлов в схеме должно быть не менее двух. Это и послужило поводом для создания и использования общекотловой автоматики, дающей экономию энергоресурсов и исключающей человеческий фактор. Общекотловая автоматики классической схемы позволяет:
— использовать ротацию котлов и насосов (поочередную работу котлов и сетевых насосов К2);
— при необходимости автоматическое включение в работу дополнительного котла.
Ротация котлов позволяет делать одинаковый моторесурс всех котлов, а ротация насосов кроме одинакового моторесурса не позволяет насосам "захряснуть". Многие производители насосов, такие как Grundfos, Wilo и др. , особенно на маломощные насосы рекомендуют использовать поочередную работу насосов или при долгом отключении насоса проводить его кратковременное включение на 1-2 минуты.
Для устранения основных недостатков классической схемы, стали вносить изменения и вводить дополнительные элементы:
1. дополнительные насосы, т.е. для повышения температуры обратного теплоносителя перед котлом, установлены дополнительные насосы на каждый котел, как показано на рисунке 2.
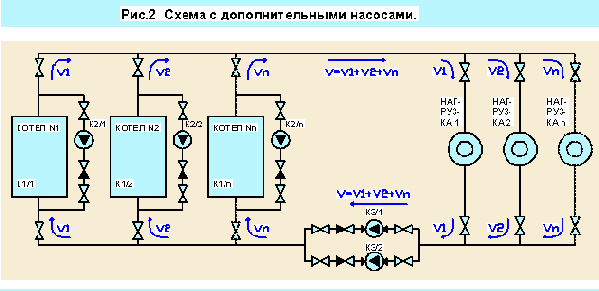
Производительность насоса К3 примерно на 30% меньше производительности насоса К2. При помощи элементов автоматики, насос К3 поддерживает необходимую минимальную температуру теплоносителя на входе котла.
Общекотловая автоматика в этой схеме (см. рис. 2) позволяет:
— поддерживать определенную минимальную температуру теплоносителя на входе котла;
— использовать ротацию котлов и сетевых насосов;
— при необходимости автоматическое включение в работу дополнительного котла.
Не достаток схемы (см. рис. 2):
— проток воды через котел имеет переменный характер;
— через выключенный котел течет теплоноситель;
2. Для качественного регулирования нагрузок котельной, применили 3-х (4-х) ходовые смесители. Это действительно оригинальное решение в гидравлических схемах котельных, смотрите рисунок 3.
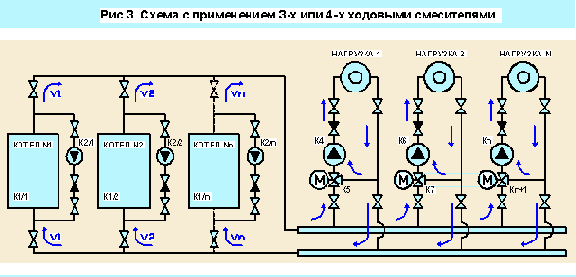
Качественное регулирование нагрузки осуществляется за счет подмешивания подающего теплоносителя от котлов и обратного теплоносителя от нагрузки при помощи 3-х (4-х) ходового смесителя и соответствующего прибора автоматики с ПИД регулированием. Температурный график теплоносителя нагрузки может быть как переменный, так и постоянный это зависит от технического задания на проектирование. Для нормальной работы этой гидравлической схемы большое внимание следует уделить котловой и общекотловой автоматике. Данную автоматику следует назвать интеллектуальной, поскольку она должна отслеживать инерционный нагрев и остывание котла на разных режимах нагрузок, в противном случае котлы часто будут перегреваться и при помощи предохранительного температурного термостата будут входить в аварию. Как правило, схему на рисунке 3 рекомендуют производители котлов и котловой автоматики такие, как Buderus, Wiessmann, De Dietrich и др. Общекотловая автоматика в этой схеме (см. рис. 3) позволяет:
— поддерживать определенную минимальную температуру теплоносителя на входе котла;
— использовать ротацию котлов и сетевых насосов;
— при необходимости автоматическое включение в работу дополнительного котла;
— погодозависимое управление нагрузками.
Не достаток схемы (см. рис. 3):
— проток воды через котел имеет переменный характер;
— через выключенный котел течет теплоноситель.
Для устранения протока сетевой воды через выключенный котел, некоторые фирмы стали отсекать котел от системы при помощи запорной арматуры с управляющим электроприводом, но это не совсем красивое решение.
3. На рисунке 4 показана гидравлическая схема, которая лишена практически всех выше перечисленных недостатков. В схему введен новый дополнительный элемент К8,
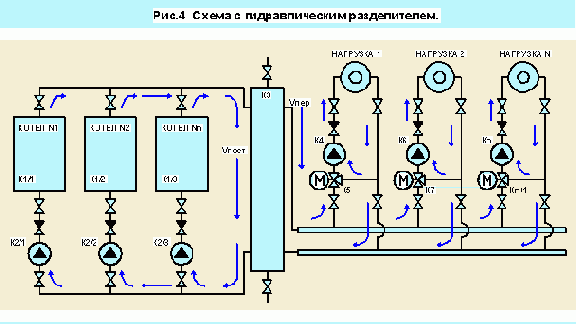
описание которого вы не найдете ни в одном справочнике и СНиП-е. Элемент К8 называют гидравлическим (термогидравлическим) распределителем или в простонародье гидравлическая "стрелка" и т.д. . В журнале АВОК за 2002г. N3 есть статья доктора технических наук П.А. Хаванова, - "Принципиальные тепловые схемы автономных источников теплоснабжения с коллекторами малых перепадов давления", где описывается гидравлический распределитель. Сам по себе гидравлический распределитель представляет собой короткозамкнутый участок, имеющий минимальное гидравлическое сопротивление и выполняет 3 функции:
1. — гидравлическое разделение котельной и нагрузки, т.е. работает золотое правило - котельная и нагрузки работают по своим правилам, не мешая друг другу;
2. — гидравлический распределитель является фильтром отстойником для крупных взвешенных частиц присутствующих в сетевой воде;
3. — гидравлический распределитель является сборником воздуха и деаэратором. Некоторые производители в своих гидравлических распределителях в верхней зоне устанавливают так называемую "отбойную доску", с множеством маленьких отверстий по всей площади.
Это помогает интенсивному выделению воздуха из сетевой воды.
Основное требование для нормальной работы гидравлической схемы, что бы объем циркулируемой воды в котловом контуре, превышал в 1/ 2 - 1/5 раза суммарный объем циркулируемой воды во всех контурах нагрузок при максимальной потребности в тепле. Скорость протока воды через гидравлический распределитель должна быть не более 0,1м3/час. Эта гидравлическая схема прекрасно управляется общекотловой автоматикой и работает она действительно как двигатель внутреннего сгорания.
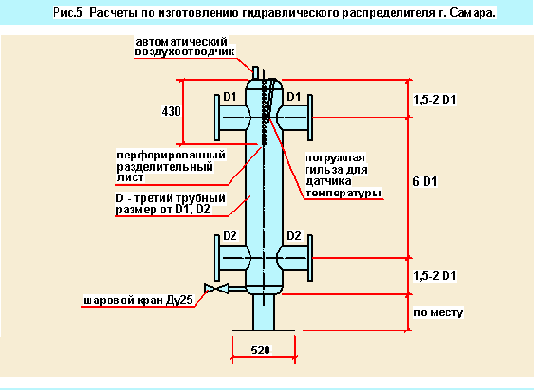
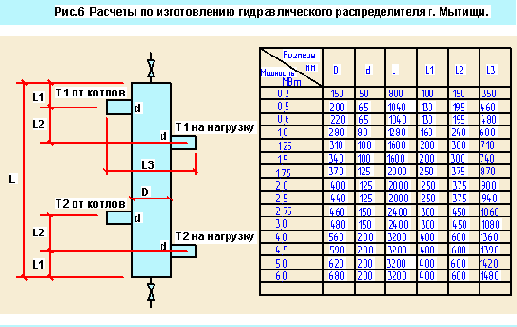
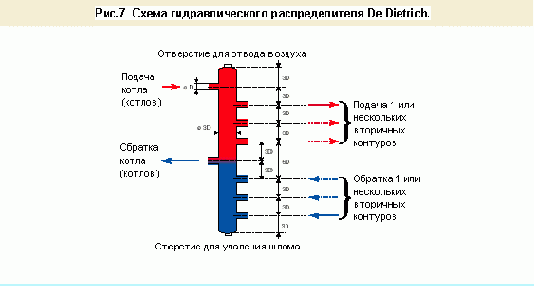
Более подробное описание общекотловой автоматики и описание гидравлической схемы показанной на рисунке 4, вы можете посмотреть по интернет адресу: http://www.sura.ru/atm/stat/stat1.html .
Фотографии котельных выполненных по схеме 4, вы можете посмотреть по адресу: http://www.sura.ru/pgk/foto.html .
Описание и работа гидравлического распределителя не плохо описана в проспекте на котлы De Dietrich, это описание можно скачать с сайта по интернет адресу: http://beg.kiev.ua/download/proect.exe . Файл proect.exe является самораспаковывающимся RAR-архивом.
В руки автора попадали еще 2 рисунка с расчетами по изготовлению гидравлического распределителя, один рисунок из г. Самары (см. рис. 5), второй рисунок из г. Мытищи (см. рис. 6) и третий рисунок из проспекта на котлы De Dietrich (см. рис. 7).
По рисункам 5, 6 и 7 видно, что идеология построения гидравлического распределителя очень похожи.
Существуют и другие решение по построению гидравлических схем, смотрите рисунок 8. Эту гидравлическую схему для своих котлов предложила американская компания "Teledyne Laars" и называется она - "Многокотловые отопительные системы с первичными и вторичными циркуляционными кольцами". Описание этой гидравлической схемы можно посмотреть по интернет адресу: http://otoplenie.com.ru/otp2/gl1.html .
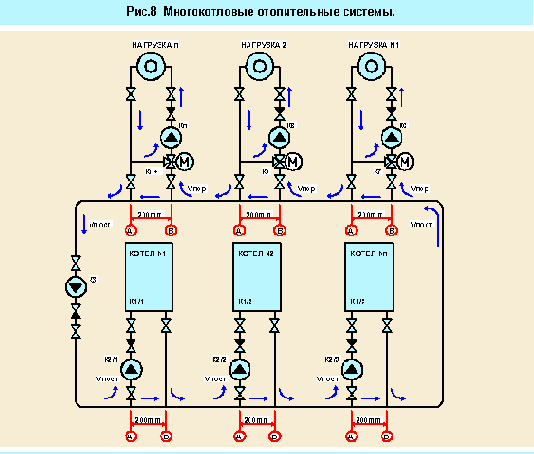
На первый взгляд эта схема коренным образом отличается от предыдущих схем, однако это совсем не так.
Обратите внимание на короткозамкнутые участки А и В, расстояние между врезок труб равно 200мм, а это и есть миниатюрные гидравлические распределители, который мы рассматривали выше, только соединены все они последовательно. Если соединить все точки А и В, то мы получим гидравлическую схему показанную на рисунке 4 и лишенную недостатков находящихся в схеме на рисунке 8. Недостатки эти видны не вооруженным взглядом, температура теплоносителя после каждой нагрузки понижается в зависимости от характера нагрузки.
Еще одна часто применяемая гидравлическая схема для приготовления ледяной воды (+1 - +4оС), смотрите на рисунке 9. Опять видно, что это не что иное, как наш гидравлический распределитель, только открытого типа и расположен он горизонтально.
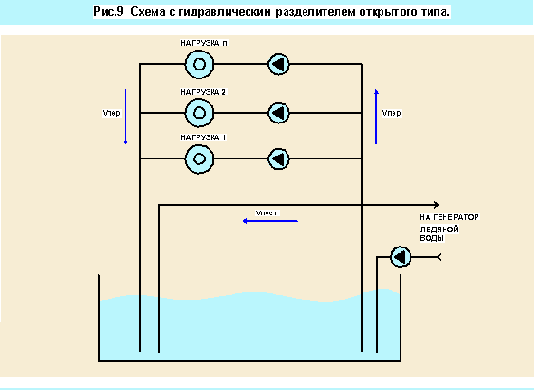
Дальнейшее развития гидравлических схем водогрейных котельных, вряд ли обойдется без гидравлического распределителя и 3-х (4-х) ходовых смесителей в контурах нагрузок.

Автоматизированная котельная, работающая без постоянного присутствия обслуживающего персонала, должна выдавать аварийные световые и звуковые сигналы об «аварийной остановке котла» и «давления в системе» (в котле) на технологическую сигнализацию и удаленную диспетчеризацию. Все современные котлы типа Buderus, Wiessmann, ACV, Ferroli и т.д., со своими горелками имеют эти сигналы в виде световой индикации на панели управления котла (авария перегрев котла), на менеджере состояния горелки (авария горелки). Сигнал аварии min-max давления в теле котла надо снять с электроконтактного манометра (далее ЭКМ), установленного на каждом котле в подающей линии до запорной арматуры. Итого имеем три сигнала, два из которых относятся к «аварии котла» и один сигнал относится к «аварии давления» в системе. Рассмотрим эти сигналы:
- Световая индикация на панели управления котла — авария перегрев котла. — Появление этого сигнала происходит от срабатывания аварийного термостата котла.
- Световая индикация на менеджере состояния горелки — авария горелки. — Появление этого сигнала происходит от неисправности датчиков или механизма самой горелки, либо отсутствия топлива.
- Сигнал min-max давления в системе — авария давления. — Появление этого сигнала происходит при понижении либо повышении давления в системе.
Первые два сигнала имеют одинаковые свойства:
а) выдают световую сигнализацию;
б) блокируют свое состояние;
т.е. для выяснения происхождения сигнала аварии, устранения неисправности и ручной разблокировки устройства требуется вмешательство человека.
Формирование третьего сигнала, — min-max давление опишем в пункте 1.2..
Но нам надо, как было написано выше, передать сигнал об «аварийной остановке котла» на технологическую сигнализацию и удаленную диспетчеризацию. Поскольку эти два аварийных сигнала при срабатывании выдают световой сигнал и блокируются (этого достаточно для визуального нахождения конкретной причины аварии), то мы их можем объединить вместе и назвать этот сигнал как «Авария котла», т.е. произошло аварийное отключение котла. Далее сигнал «Авария котла» надо подать на схему (шкаф) технологической сигнализации, где включится соответствующая световая и звуковая сигнализация, свидетельствующая о неисправности технологического процесса. При поступлении на схему технологической сигнализации
любого аварийного сигнала технологического процесса, его можно передать на удаленную диспетчеризацию
как чисто по физическому кабелю, так и при помощи GSM модема.
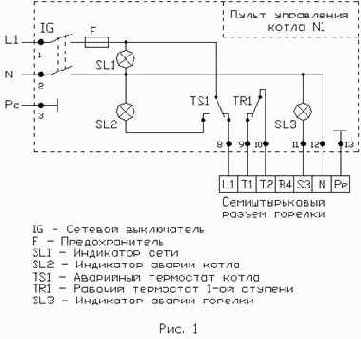
На практике это выглядит так: на рис. 1 мы видим схему типового термостатического пульта управления котла. Данная схема используется практически на всех котлах, а на котлах таких производителей как Buderus, Wiessmann и т.п., на данную схему накладывается еще и дополнительная схема автоматического управления котлом.
Сигналы авария котла и горелки, как видно по схеме, это световые индикаторы SL2 и SL3, во время сигнала аварии на них подается напряжение 220в. Объединения двух сигналов авария и преобразовании уровня сигнала с 220в на +24в (требуемый потенциал для технологической сигнализации) с гальванической развязкой, можно подключив параллельно к каждому индикатору SL2 и SL3 промежуточное реле типа РП-21.
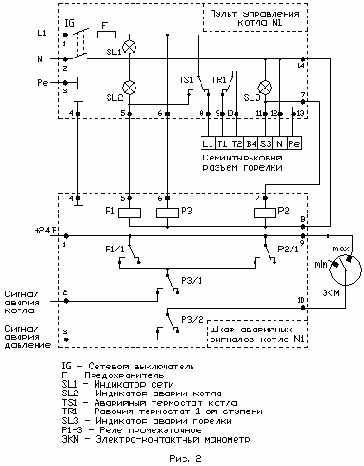
На рис.2 мы видим схему соединений «Пульта управления котла N1» и «Шкафа аварийных сигналов котла N1». Контакты P3/1 промежуточного реле P3 установлены для того, что бы во время отключения котла (например для ремонта) его аварийные сигналы были отключены от общей котловой автоматики. Подключение следующего котла к общекотловой автоматике осуществляется аналогично, см. Рис. 3.
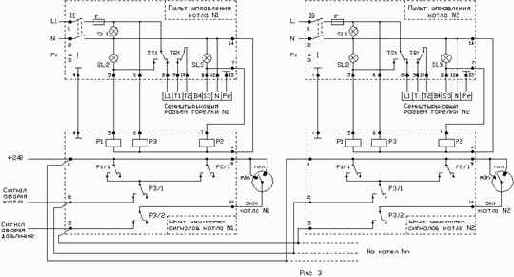
1.2. ЭКМ установленный на каждый котел выполняет две функции, это визуальный контроль давления и электрические сигналы аварийного давления в котле. Для контроля min-max давления в котле целесообразно в шкаф «Аварийных сигналов котла» ввести сигналы с ЭКМ через контакты P3/2 промежуточного реле P3. При отключении котла сетевым выключателем для регламентных (ремонтных) работ, контакты реле P3/2 разомкнутся, что предотвратит появления сигнала «Авария давление» во время опорожнения котла.
Куликов В.Н.
E-mail: atm@sura.ru.

Манометры устанавливаются на трубопроводы через 3-х ходовой кран, как показано на рисунке 1.
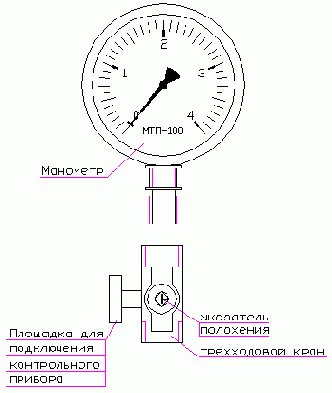
Рис. 1
На рисунке 2 видно, что наш "родной" трехходовой кран для манометра незаменим. Он имеет целых 5 рабочих положений.
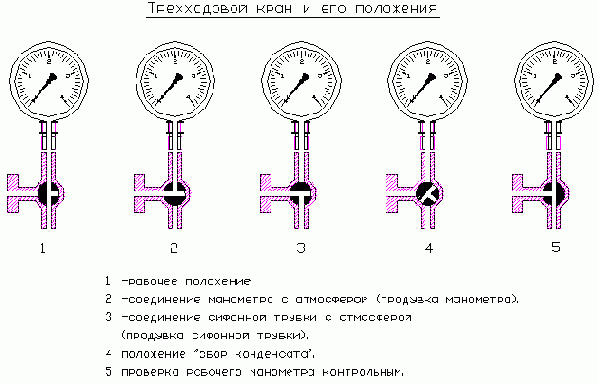
Рис. 2
По рисунку 3 видно, что одним манометром можно последовательно замерить 3 точки показания давления. Это не только существенное сокращение количества измерительных приборов в котельной, (которые надо ежегодно поверять) но и упрощение в монтаже.
Одну подводку к манометру можно жестко зафиксировать "черняшкой" с установкой на ней крестовиной, 3-х ходового крана и манометра, остальные две точки можно подключить гибкими бронированными подводками. Такое подключение манометра позволяет более точно замерить сопротивление нагрузки и перепад давления у насоса, даже если манометр "врет". Ведь во всех трех точках манометр будет "врать" одинаково.
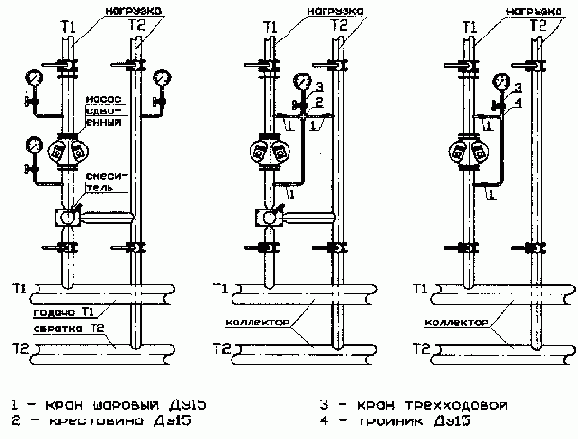
Рис. 3
Гибкая бронированная подводка рисунок 4.
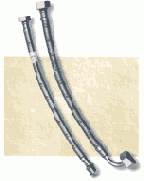
Рис. 4
Кроме того, не забывайте пожалуйста, измеряемая среда должна иметь температуру не более 70°С, если температура измеряемой среды выше, то следует устанавливать перед манометром специальные отводы (см. рис. 5).
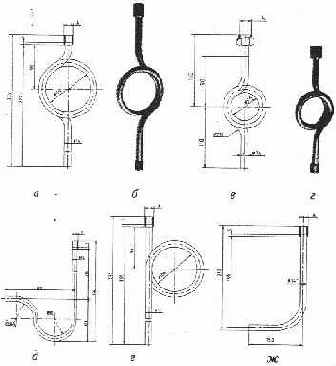
Рис. 5
Схемы и виды сифонных отводов, применяемых для подключения манометров к трубопроводам и сосудам с измеряемыми средами: а, б, в, г - петельный центральный большой (ОС100) и малый (ОС56); д - боковой с коленом (ОС100-02); е - петельный боковой (ОС100-01); ж - угловой (ОС100-03).
Рабочие параметры (МПа): давление <40.
Наружный диаметр трубки: 14мм.
Присоединительная резьба: М20х1,5.
Отводы изготавливаются с наружной и внутренней резьбой.
Материал отводов: Сталь 20 ГОСТ 8734-75.
Куликов В.Н.
E-mail: atm@sura.ru.